Polyurethane Machinery
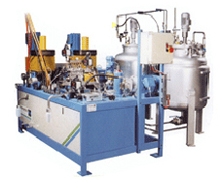
Since Polyurethane occurs by a reaction of two components, a machine is required to dose, mix and at the end pour to mould (or to free zone) these two components. Components that are concealed in day-tanks of machine in desired temperature, are forwarded simultaneously to mixing chamber in mix-head and poured from the mix-head immediately. Since mixing components starts a chemical reaction, all these processes take place in a quite short time in the form of consecutive steps.
In Polyurethane Technology, there are “Low Pressure Machines” which are running in 0-15 bar working pressure and “High Pressure Machines” that are running in 100-200 bar working pressure. Since mixing quality is insufficient in former, there are additional mechanical stirrers in mixing chambers. After the shot, mixing chamber is flushed with a solvent to clean residual PU Material in mix-head. In High Pressure Machines on the other hand with a driving force of 150-200 bars, particles of the two components strike to each other in a small mixing chamber (impingement mixing) which results in high quality mixing. For that reason, neither mechanical stirrer nor cleaning solvent is required. Mixing quality is perfect and production is much more speedy.
It should not be thought only dosing machines but should also be considered mould carriers, oval conveyors/carousels, robots, safety systems, climate conditioning… shortly a complete production line which is in harmony by every points when Polyurethane Machinery is mentioned.